String Potentiometer Sensor | FUTEK
What is a String Potentiometer Sensor?
A string potentiometer is a linear position sensor, also known as a string pot, draw wire position sensor, Cable Extension displacement transducer, or a yo-yo pot. It is a cable-actuated position or displacement transducer utilized for linear position measurement and velocity using a flexible cable (string) and a spring-loaded spool.
Draw wire sensors are low-cost, compact linear transducers that accurately measure the position, change in position, or velocity of objects.
Core elements of a String Potentiometer Transducer are a precision measuring wire and a sensor element (e.g. high precision potentiometer or encoder), which convert the wire linear displacement into a proportional electrical signal via the potentiometric voltage divider. The maintenance-free draw wires are particularly quick and easy to assemble and are used because of their reliability in all areas of industry.
How does String Potentiometer Sensor work?
String pots or cable-extension transducers are composed of four main components inside the housing:
- Flex High Strength Stainless Steel Cable (string or wire rope);
- Constant Diameter Spool (drum);
- High Torque, Long-life Power Coil Spring;
- Rotational Potentiometric Precision Sensor.
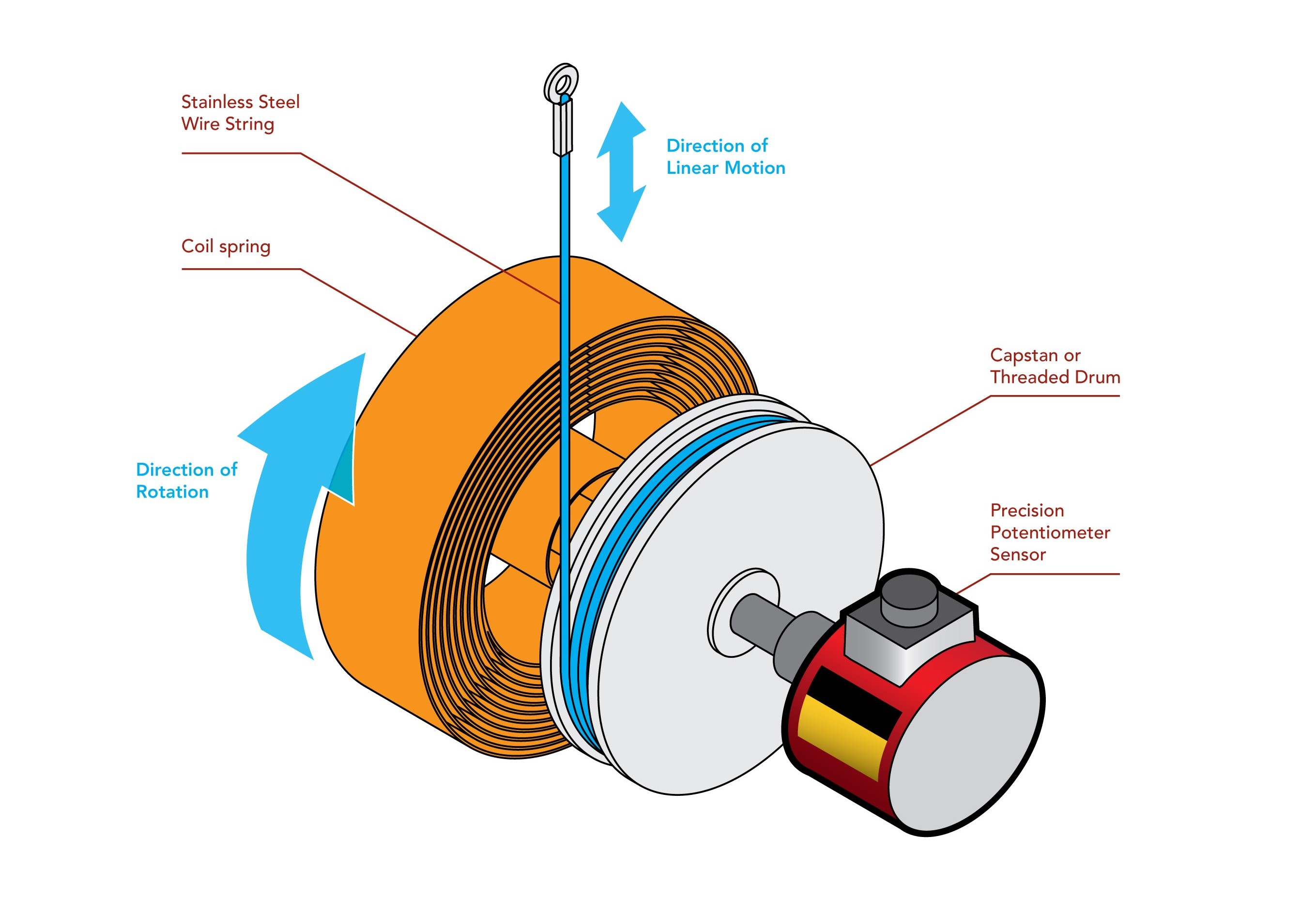
Inside the transducer's housing, a flexible high strength stainless steel cable is wound tightly around a precisely machined constant diameter cylindrical drum (or spool) that turns as the measuring cable reels and un-reels. To maintain wire tension and retraction, a spring is coupled to the drum. The spool is then coupled to the shaft of a rotational potentiometric precision sensor (or an encoder). As the sensor string extends linearly along with the moving object, it causes the drum and sensor shafts to rotate.
In order to take displacement or position measurements, the sensor’s body is mounted to a fixed surface and the end of the flexible cable is connected to the object in motion. As the object changes its positions, the cable un-reels and reels and the rotating spool drives the shaft of the sensing device generating an electrical signal that is proportional to the cable's linear extension or displacement. For speed measurement, a tachometer is required.
The draw wire displacement sensor can be hooked up as a three-wire tapped potentiometer (voltage divider) or can be packaged with embed electronics to produce an output signal in a useful form, such as a variable voltage 0-10 VDC, variable current 4-20mA, pulse encoder, Fieldbus (Profibus, DeviceNet, and Canbus) and RS232 / RS-485 communications. The sensor output signal can then be sent to a signal conditioner for amplification, local display or readout, a PLC or data acquisition system (DAQ).
What advantages do String Potentiometer Transducers have?
Measuring the displacement and speed of moving objects is a simple task with draw wire sensors. String potentiometers have a very easy and intuitive installation and do not require a specialist to do so. Due to the flexibility and high strength of the cable, it can be fitted into precarious or tight areas and they do not require perfectly parallel alignment.
An obvious benefit of draw-wire measuring principle is that the measuring cable can be diverted over deflection pulleys. This characteristic differentiates string pot sensors from other linear displacement measurement principles which normally only measure on one axis. Moreover, as the sensor housings are is extremely compact, it enables large measuring ranges to be performed with a relatively very small transducer body, saving assembly space in your application.
String pots also offer great space flexibility as their housing size to measurement ratio it is higher than LVDT Linear Displacament Transducers, for example, and they normally are more cost-effective when compared to other linear position measurement technologies given the simplicity of the transducer operation.
Draw wire Transducers are selected for linear motion measurement as it presents the following advantages:
- Fast and easy assembly - can be installed in minutes without the need of an expert;
- Can fit into small spaces and relatively very good sensor size to measurement ratio - suitable for applications with constrained space or difficult to access locations;
- Given the flexibility of the wire rope, do not require perfect parallel alignment between the sensor body and the moving object to function accurately;
- Cost-effective linear displacement measurement option compared to alternatives;
- Suitable for displacement, distance, and position measurement from 25mm to 50,000 mm;
- High measurement resolution;
- High operational safety and extended service life;
- Analog and digital outputs.
What are the applications for String Potentiometers?
Draw wire sensors are utilized to measure the position or displacement of a moving part. The measurement cable is attached directly to the moving object, giving a constant measurement of its linear position. This is a reliable position measurement technology and has proven to be effective by engineers and designers over the past four decades. String potentiometers are generally durable, simple to use, and inexpensive.
These sensors do not need precise linear guidance and are ideal for wet, dirty, or outdoor environments and applications where your measuring range travels through or hard-to-reach places. These include a broad variety of applications:
- factory automation and industrial machinery;
- medical devices and surgical robotics;
- structural civil engineering testing;
- automotive and aerospace testing;
- die-casting or injection molding;
- Telescopic applications
- oil and chemical;
- robotics;
- hydraulic cylinder position measurement and control
- just about anything moving object whose position is to measured.
What are the limitations of String Potentiometer Transducers in displacement measurement?
Since the measuring cable may sag or be deflected by wind or gravity, the environmental conditions and orientation of the assembly must be considered in order to maintain the overall precision of a string potentiometer measurement.
The un-reel / reel cable-spool mechanism limits the speed at which the measured object can move. Changing temperatures affect both the length of the cable and the resistance value of the potentiometer, so additional temperature compensation devices must be employed in these scenarios.
Where multiple objects, such as articles on an assembly line, or objects that are hot or coated with wet paint are to be measured, a non-contacting method is preferred.
Other linear position measurement methods include LVDT, LVIT, strain-gages, potentiometric, capacitive, optical (time of flight), and magnetic-inductive transducers.
This page is for information only. FUTEK instruments can be used with potentiometers supporting the appropriate input range of our instruments, however FUTEK does not sell string potentiometer sensors.