UART and SPI are both commonly used in embedded system designs and developments due to their simplicity and ease of operation.
UART (Universal Asynchronous Receiver Transmitter):
UART is a widely-used serial communication protocol in embedded systems. It operates by transmitting data one bit at a time sequentially over a communication channel. Common serial communication protocols include RS-232, RS-485, USB (Universal Serial Bus), and SATA (Serial ATA).
- UART typically employs two wires: one for transmitting data (TX) and one for receiving data (RX). For higher-speed communication, it’s advisable to use four wires, including Request to Send (RTS) and Clear to Send (CTS) lines.
- UART communication is asynchronous, meaning the devices involved do not share a synchronized clock signal; they operate independently.
- UART is suitable for long-distance communication.
Load cell amplifiers can benefit from UART communication when connecting load cells to microcontrollers or computers, enabling precise data transmission over long distances without the need for synchronized clocks. UART is often used as a form of device-to-device communication in computer and microcontroller applications.
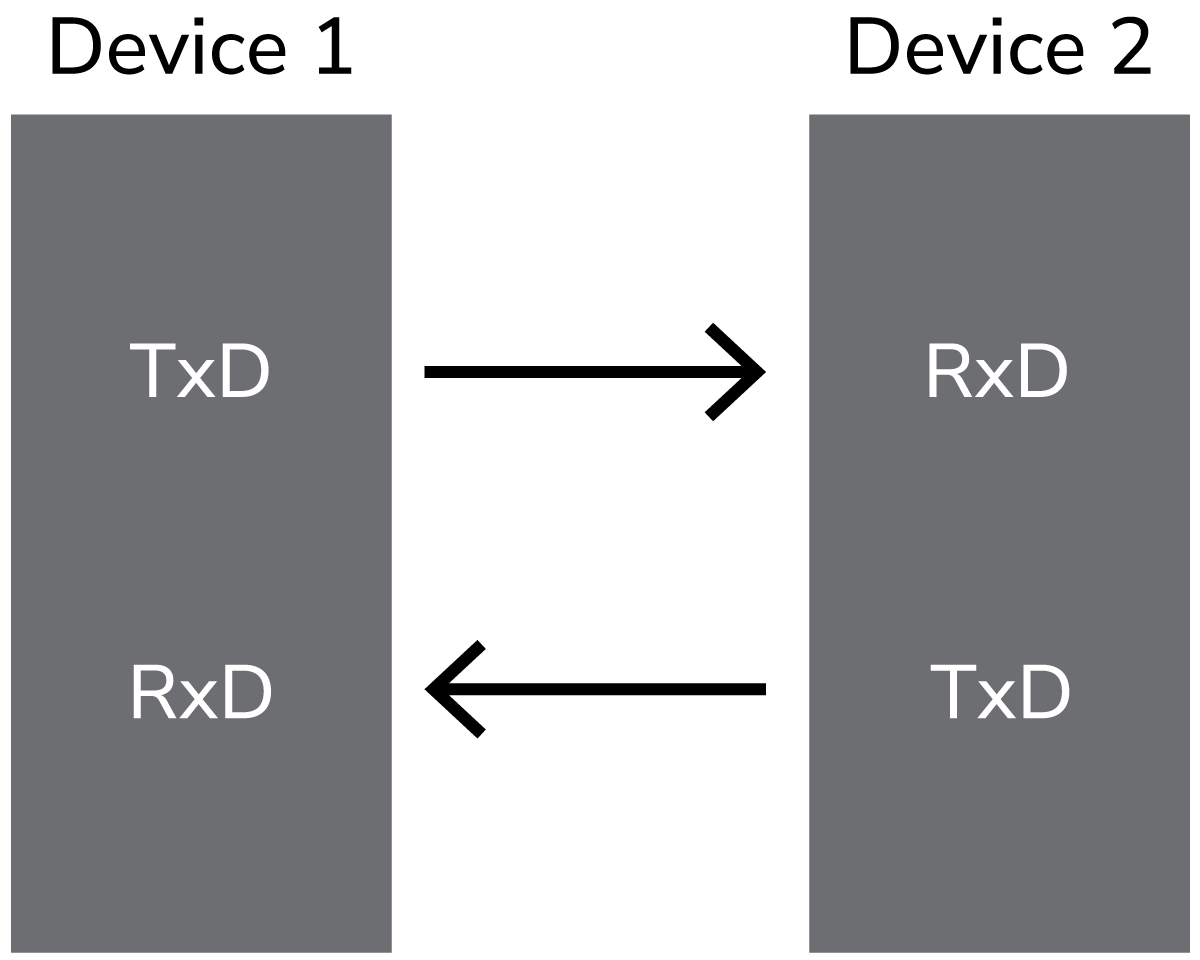
SPI (Serial Peripheral Interface)
SPI is another serial communication protocol that facilitates data exchange between various electronic devices supporting clocked serial streams. SPI follows a Host-Client communication approach, allowing high-speed data transfer. It is known for its efficiency and low overhead, making it ideal for high-speed data transfer in applications like load cell signal conditioning.
- SPI typically uses four wires: System Clock (SCLK), Host Output/Client Input (HOCI), Host Input/Client Output (HOCI), and Chip Select (CS) signal pin.
- SPI is a synchronous communication protocol.
- SPI is known for its efficiency and low overhead, making it ideal for high-speed data transfer.
- SPI supports full-duplex communication, enabling simultaneous data transmission between the host and client.
- SPI is designed for short-distance applications and supports high communication speeds. Strain gauge signal conditioners can effectively utilize SPI for precise and rapid data transfer.
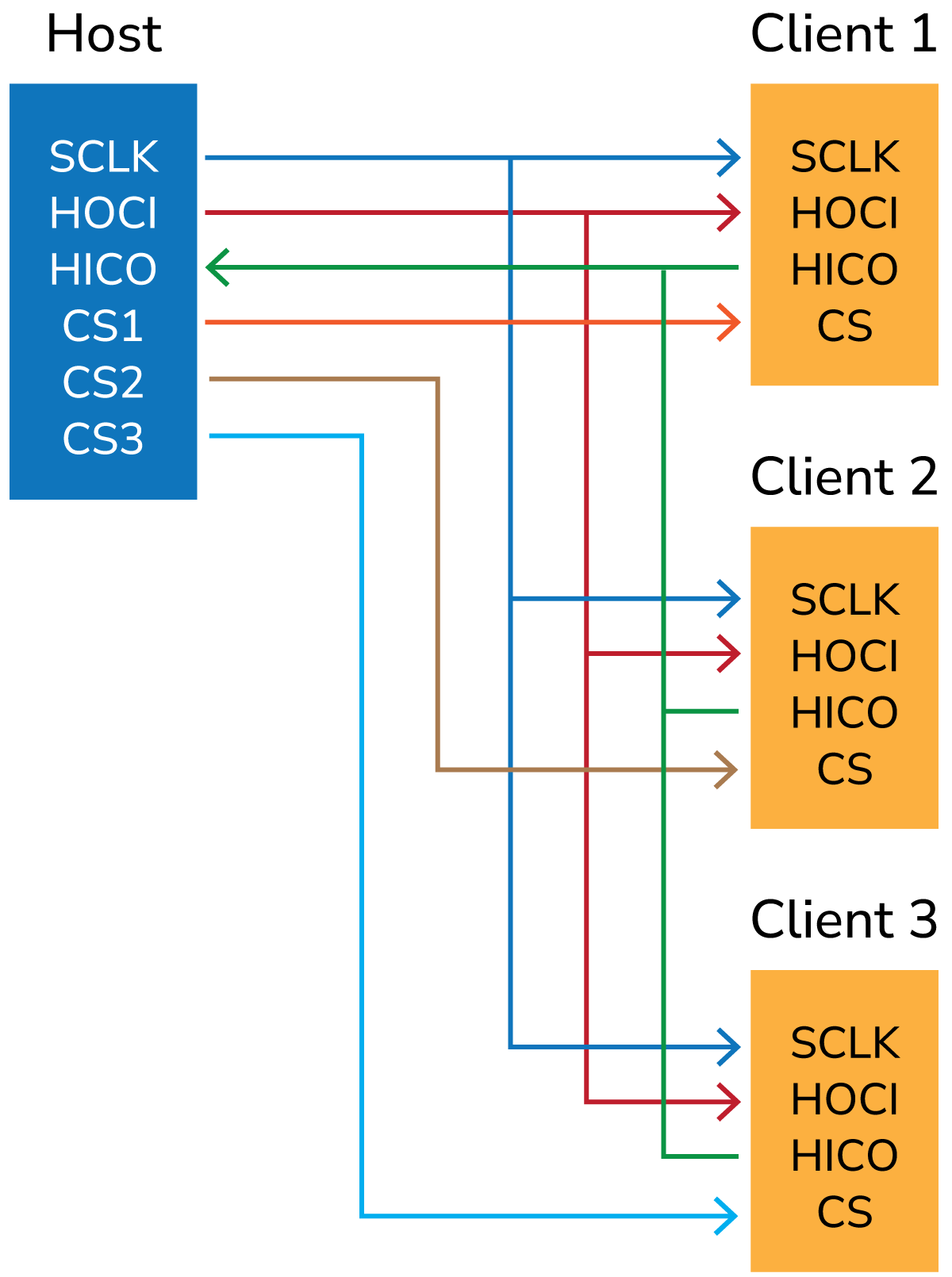
UART vs. SPI
- SPI is preferred for high-speed communication between chips or when connecting multiple devices over short distances. It is especially beneficial for applications such as load cell signal conditioning due to its high-speed capabilities.
- UART is more suitable for applications requiring longer-distance communication.
- Unlike SPI, UART is a physical circuit and relies on two UART devices to send and receive data. It doesn’t use a shared clock, so baud rates must be closely matched to avoid data loss.
- Both UART and SPI do not support multi-host configurations, but SPI offers significantly higher data transfer speeds compared to UART.
In summary, the choice between UART and SPI depends on the specific requirements of your embedded system, with SPI offering higher-speed communication over shorter distances, while UART is better suited for longer-distance applications and can be beneficial for load cell amplifiers, strain gauge amplifiers, load cell signal conditioners, and strain gauge signal conditioners.
UART vs. SPI | ||
---|---|---|
Parameters | UART | SPI |
Type | Hardware (physical circuit) | Protocol |
Minimum Number of Pins | 2 | 3 |
Number of Devices | One-To-One Communication | Multiple Devices |
Communications Speed | ~6.25Mbaud | ~100 MHz |
Communication Type | Asynchronous | Synchronous |