Digital Load Cell | Digital S-Beam Jr.® Miniature Load Cell 3.0
> LSB206
Fully digital output in a miniature package
The LSB206 is a miniature S Beam Jr.® load cell that offers fully digital SPI and/or UART output in a tiny package. It is a high-performing all-in-one solution with embedded ultra-low-power, ultra-miniature electronics that convert analog signal to digital output, removing the need for an external amplifier and analog-to-digital converter. The LSB206 has M3x0.5 female threads and offers built-in up to 10x overload protection in both directions of tension and compression.
This remarkably small load cell communicates directly with microcontrollers via UART or SPI bus in embedded applications, which opens up possibilities for usage in high-volume PLC, automation, and system integration applications.
Compact package and low power consumption
With dimensions of 0.75in [19.05mm] in height and 0.38in [9.5mm] in width and low power consumption of 78mW, the highly compact LSB206 sensor is an ideal candidate for any spaces with tight assembly requirements as well as densely packed and/or battery-powered applications.
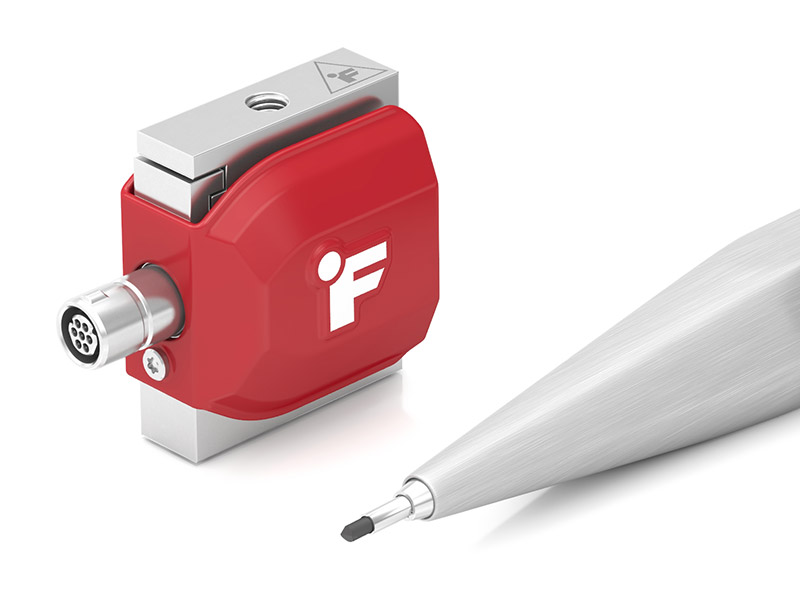
Selectable sampling rate
Despite its compact size, the LSB206 delivers impressive performance with a wide selection of ranges and support of sampling rates from 4 Samples per seconds (SPS) to 1,300 SPS. This offers unique flexibility in a variety of system integration applications. The model is capable of outputting up to 15 Bits of Noise Free Resolution (NFR).
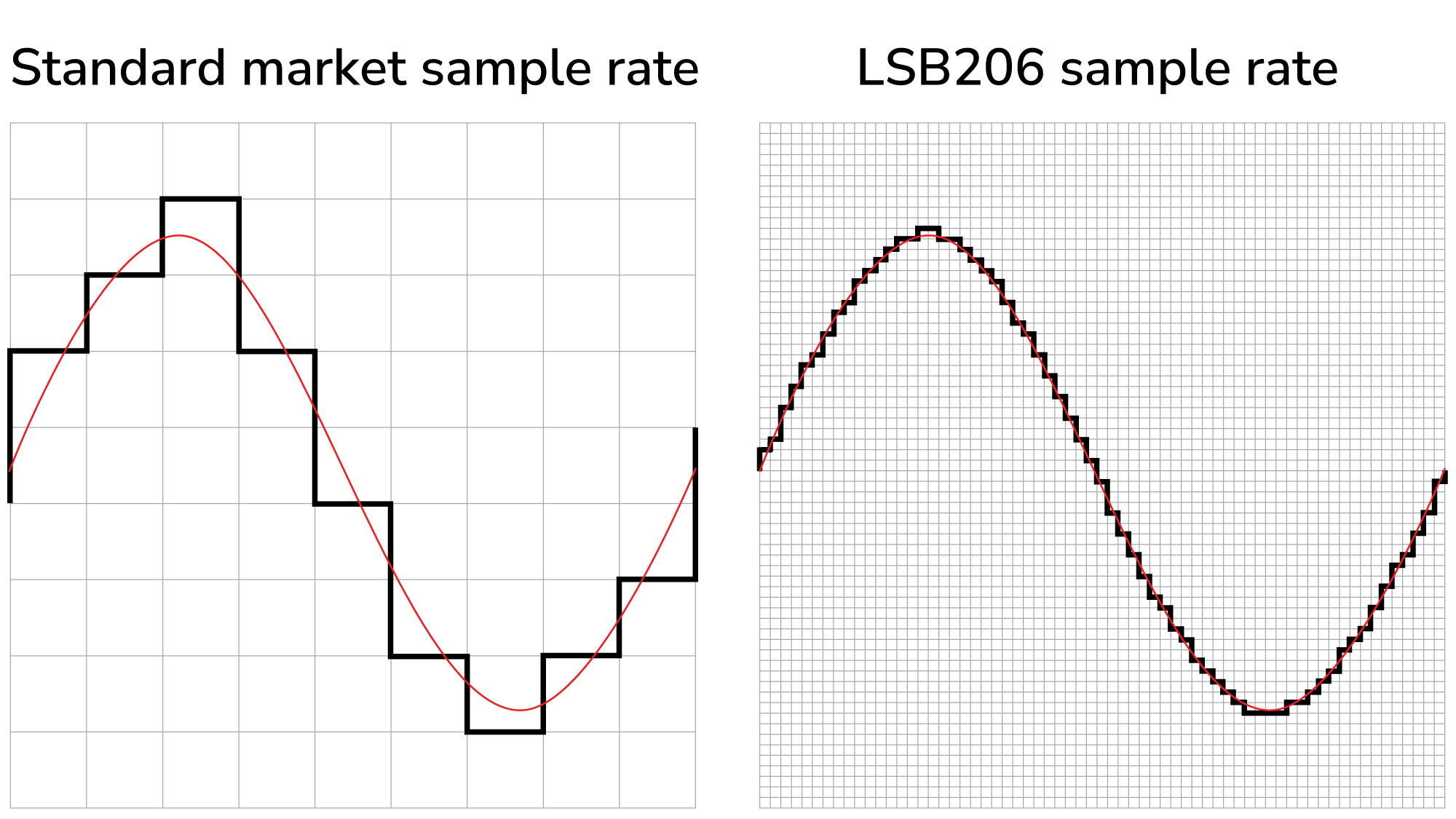
Highly configurable output
The LSB206 is controllable through commands via UART and SPI with implemented error detection algorithms (Custom Checksum and Cyclic Redundancy Check (CRC8)) Its internal onboard memory stores calibration data and low inrush current (max 400 mA) enables stability and low power consumption. It also has very low nonlinearity (±0.1% of FSR).
Overload protection
The LSB206 is rated for 10x overload protection for tension and compression (1-25 lbs) and 2x tension overload protection (50-100 lbs). This prevents sensor damage from direct inline overloads that could occur during the setup process or the occasional system over-range.
Optional SPI/UART output
The LSB206 model is offered in two versions. One has access to both SPI and UART outputs depending on user preference, the other has UART protocol only. SPI is a synchronous protocol that is preferred in applications that require higher-speed communication or applications that require communications between multiple devices in relatively short distances. UART is an asynchronous protocol that is better suited for applications that need to travel a slightly longer distance.
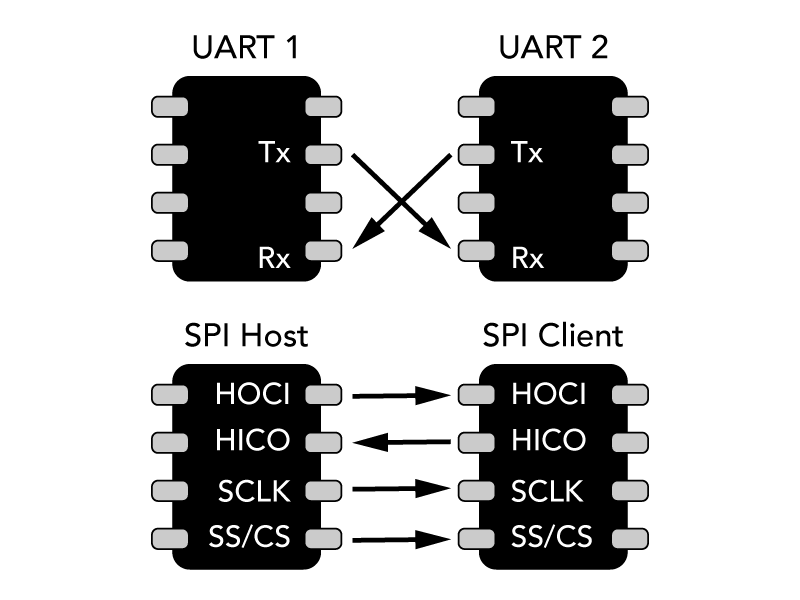
SPI/UART with robust cable
The SPI/UART version of the LSB206 is powered by a 32 AWG 10 conductor spiral shielded cable with a silicon jacket that is 6 in [152 mm] long. It features a robust mechanical strain relief for low noise operation even in a highly dynamic environment.

UART with plug-in connector
The UART-only version of the LSB206 load cell has an aerospace- and military-grade 7-pin Nano connector that allows for easy and simple cable connection and disconnection. This version can be used for distances up to 15ft (4.57m) and is easy to set up and run in applications such as R&D testing. A damaged sensor cable can be replaced without having to replace or disassemble the LSB206 sensor or any other system component, which saves time, leads to higher system availability, and reduces the total cost of ownership. It also simplifies the installation process, reducing installation time and maximizing up-time.
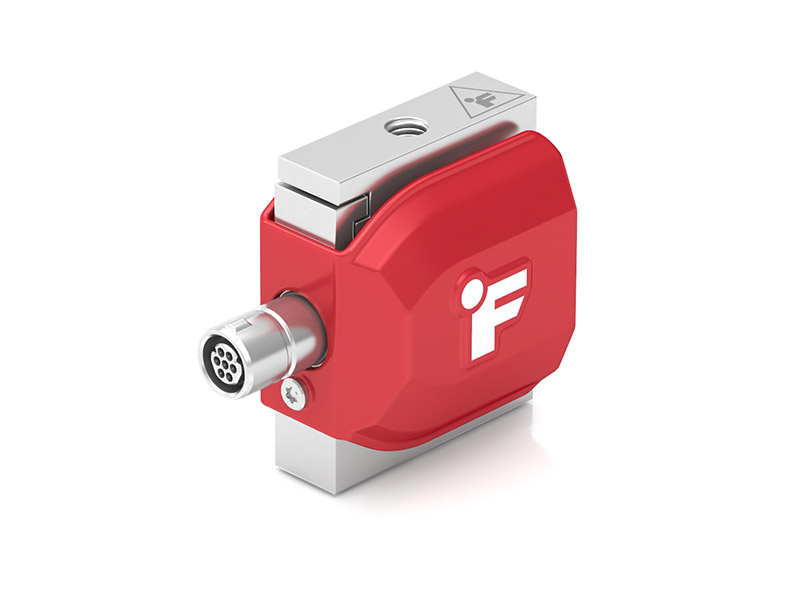
Durability
Unparalleled quality and robust construction make the LSB206 extremely resilient and long-lasting. The sensor has been tested to 100 million fully reversing fatigue cycles without failure. It has also been designed with a very high level of intrinsic durability for higher system uptime and a significantly longer operational life.
High shock resistance
With an exceptional 500 G level shock resistance and 2000 Hz vibration resistance, the LSB206 can be used in high shock and high vibration applications such as in drilling, structural monitoring units in earthquake-prone areas, bridges, rail tracks, airplanes, ships, turbines, reactor vessels, and space vehicles.
Best-in-class material
The flexure of LSB206 is made from aerospace quality 17-4 precipitation-hardened stainless steel, one of the best material options for load cells. It provides high strength, high hardness, and corrosion resistance over a wide temperature range. It also enhances this tiny sensor’s ability to handle extraneous forces. A special heat treatment process has been applied to the flexure to improve strength, fatigue properties, and sensor performance.