Resources › What are load cells made of?
Whether you are looking at one of our load cells, pressure sensors, or torque sensors, they are all constructed from a metal body with strain gauges wired at critical points to measure loads. We most commonly construct our sensors from aluminum or stainless steel, depending on the maximum capacity of the sensor.
The strain gauges are thin metal wires bonded to a thin plastic base. These gauges are then bonded and wired onto key locations of the load cell. As the sensor is subjected to load, those locations accurately transmit the load, or strain, to the strain gauges. The wire length in the gauge then changes, altering the resistance proportionally based applied load.
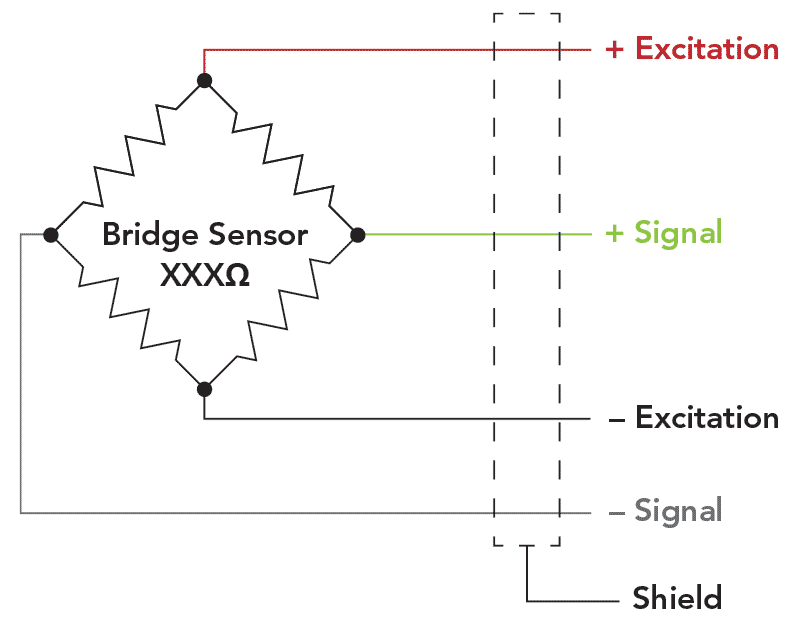
The strain gauges are then wired together with balancing gauges to form a full Wheatstone bridge. With a completed bridge, an excitation voltage is applied to two opposite points of the sensor. You then measure the voltage difference between the other two points of the sensor, the signal points. When the sensor is at rest, the voltage difference between the signal points is effectively zero. As a load is applied to the sensor, the resistance across the Wheatstone bridge changes. This creates a measurable change in voltage between the two signal points which has a linear relationship to the load applied.